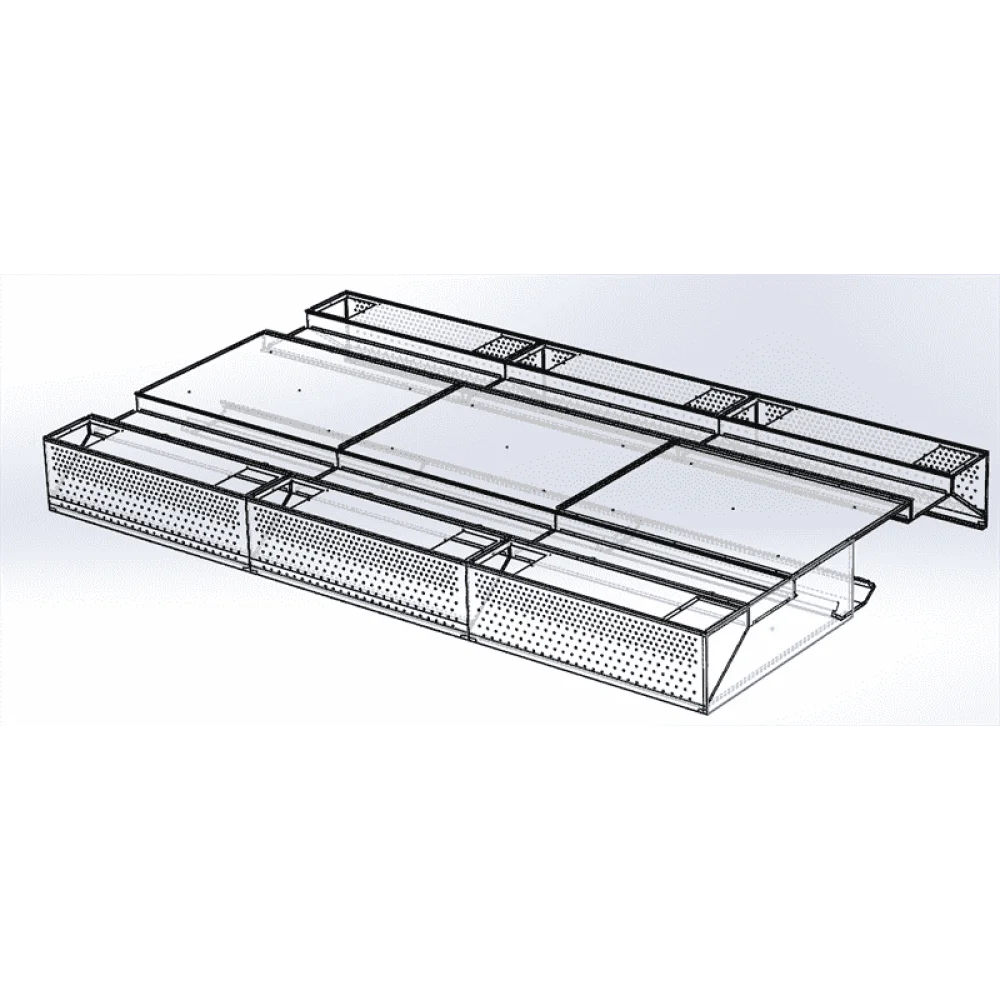
Comprehensive Ventilation and Material Solutions for Battery Charging Areas and Hydrogen Handling Facilities
Introduction
In industries where battery-powered forklifts, pickers, and hydrogen-based technologies are prevalent, maintaining safe operational environments is paramount. Hydrogen, whether released during battery charging or as part of testing new fuel powertrains, poses unique safety challenges due to its highly flammable nature and the risk of hydrogen embrittlement in metals. To address these challenges, eCanopy offers comprehensive ventilation and material solutions designed specifically for environments handling hydrogen gas. Our solutions are ideal for B2B mechanical contractors, logistics operators using battery-powered machinery, and testing facilities exploring hydrogen in energy applications.
Why Ventilation and Material Selection Matter
Hydrogen Risks in Battery Charging Areas: Battery charging areas, particularly those for lead-acid batteries, are prone to hydrogen gas release during the charging process. Accumulation of hydrogen in confined spaces can create explosive atmospheres, posing significant safety risks to personnel and equipment. Adequate ventilation is critical to disperse hydrogen gas, prevent dangerous concentrations, and comply with health and safety regulations.
Hydrogen in Emerging Technologies: Hydrogen is increasingly being explored as a clean energy source, mixed with natural gas, or used in new fuel cell powertrains. While promising, hydrogen's interaction with metals can lead to hydrogen embrittlement, a process that compromises material integrity. This risk is especially pertinent in testing facilities, research and development centers, and industries transitioning to hydrogen fuel systems.
Our Solution: eCanopy provides tailored ventilation systems and expert guidance on material selection to ensure safe, efficient, and compliant operations in environments where hydrogen gas is present. Our solutions cater to various applications, from battery charging areas to advanced hydrogen research and testing facilities.
Ventilation Solutions for Hydrogen Safety
1. Customized Ventilation Systems for Battery Charging Areas
For battery charging rooms, it’s essential to prevent hydrogen accumulation through effective ventilation strategies. We offer customized ventilation systems designed to meet the specific needs of your facility, ensuring optimal safety and regulatory compliance.
Key Features:
- Optimized Air Change Rates: Our systems are designed to achieve 6 to 12 air changes per hour (ACH), depending on your specific requirements. For most battery charging areas, we recommend a ventilation rate of approximately 8 ACH, translating to a flow rate of 420 m³/hour for typical room dimensions of 7,000 mm x 3,000 mm x 2.5 m.
- Local Exhaust Ventilation (LEV): To capture hydrogen gas at the source, our LEV systems offer extraction rates between 0.3 to 0.5 m³/min per charger, ensuring localized capture and safe dispersal of hydrogen outside the building.
- Hydrogen Detection and Safety Systems: Our integrated hydrogen sensors continuously monitor gas levels, providing real-time alerts to ensure immediate response if gas concentrations approach unsafe levels.
2. Ventilation Solutions for Hydrogen Testing and R&D Facilities
For facilities exploring hydrogen as a fuel source, whether mixed with natural gas or in pure form for new powertrain testing, our ventilation solutions offer robust safety features tailored to the complexities of hydrogen handling.
Key Features:
- High-Flow Ventilation Systems: Designed to handle higher concentrations of hydrogen, our systems provide adjustable air change rates to suit dynamic testing environments, from small-scale lab settings to larger industrial test bays.
- Scalable LEV Systems: For direct extraction at points of hydrogen release, our scalable LEV systems adapt to various equipment configurations, ensuring flexible and efficient gas management.
- Redundancy and Fail-Safes: We incorporate redundancy and fail-safe measures in our ventilation designs, such as backup fans and automated shutdown protocols, to maintain safety even in unforeseen circumstances.
Material Selection to Prevent Hydrogen Embrittlement
Hydrogen embrittlement is a serious concern when working with hydrogen gas, as it can compromise the integrity of metals, leading to cracks and failures under stress. Our expertise in material selection helps mitigate this risk, ensuring the longevity and reliability of your equipment and infrastructure.
Materials Prone to Hydrogen Embrittlement:
- High-Strength Steels: Particularly susceptible to hydrogen embrittlement, especially those with tensile strengths above 1000 MPa.
- Nickel-Based Alloys: While resistant to corrosion, some nickel alloys can be vulnerable to hydrogen-induced cracking.
- Titanium Alloys: Certain titanium alloys, though less susceptible than steels, can still be at risk under severe hydrogen exposure.
Recommended Materials:
- Austenitic Stainless Steels (300-Series): Grades such as 304 and 316 offer excellent resistance to hydrogen embrittlement due to their face-centered cubic (FCC) structure, making them ideal for applications in hydrogen environments.
- Aluminum and Copper Alloys: Generally immune to hydrogen embrittlement, these materials are suitable for various fittings, piping, and components in hydrogen handling systems.
- Polymer Materials: Non-metallic options like Teflon, polyethylene, and other polymers are recommended for gaskets, seals, and insulation, as they are unaffected by hydrogen.
Additional Material Considerations:
- Surface Treatments: Applying coatings like cadmium, zinc, or nickel can create barriers that reduce hydrogen permeation into metals. However, care must be taken to avoid hydrogen-introducing processes such as certain plating and pickling methods.
- Heat Treatments: Post-manufacture baking (typically at 190°C to 220°C) can effectively release absorbed hydrogen from susceptible materials, reducing the risk of embrittlement.
- Design Strategies: Our design guidance minimizes stress concentrators, such as sharp corners and notches, which can exacerbate hydrogen embrittlement. We focus on smooth transitions and rounded geometries to enhance material resilience.
Benefits of Choosing eCanopy
1. Expertise in Hydrogen Safety: With years of experience in the industry, our team brings deep expertise in hydrogen safety, ventilation, and material science, ensuring that your facility not only meets but exceeds safety standards.
2. Customized Solutions: We understand that each facility has unique requirements. Our solutions are fully customizable, tailored to the specific operational needs of your business, whether you're managing a fleet of battery-powered forklifts or pioneering hydrogen fuel technologies.
3. Compliance and Peace of Mind: Our systems are designed with compliance in mind, adhering to all relevant safety regulations and standards. With [Your Company Name], you can operate with confidence, knowing that your hydrogen management systems are both safe and efficient.
4. Continuous Support: We offer ongoing support, from initial consultation and design through installation and maintenance. Our commitment to your safety doesn't end at delivery; we are your partner in maintaining a safe working environment.
Industries We Serve
- Logistics and Warehousing: For companies using battery-powered forklifts and pickers, our solutions provide safe and effective management of hydrogen emissions during charging.
- Hydrogen R&D and Testing Facilities: We cater to research centers, universities, and private companies involved in hydrogen fuel testing, offering tailored systems for managing hydrogen in controlled and variable environments.
- Manufacturing and Industrial Facilities: Our expertise extends to any industrial setting where hydrogen is used, whether in processes, fuel cells, or experimental powertrains.